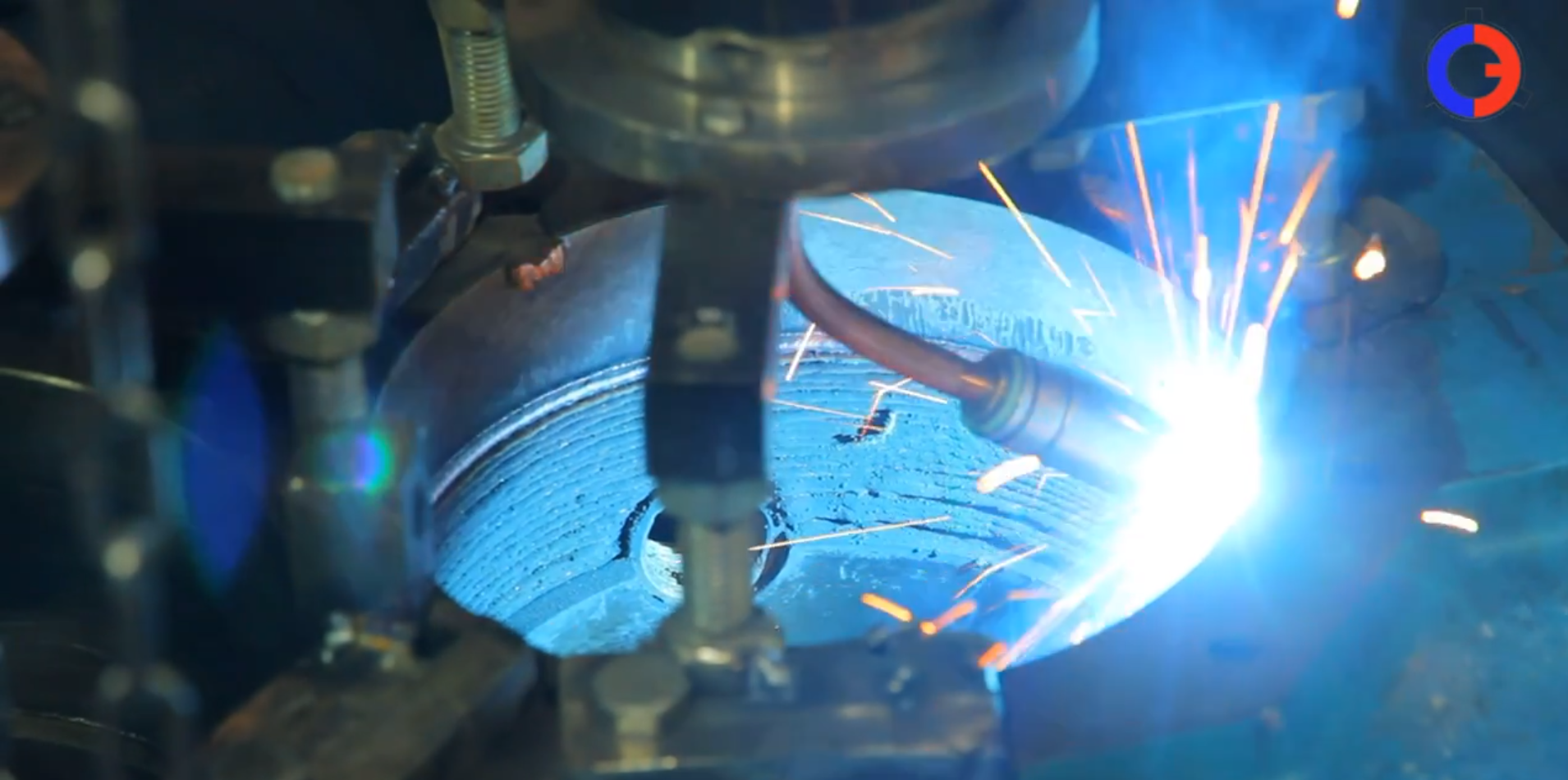
Частично механизированная сварка
Механизированная сварка (наплавка) – это технологический процесс, при котором расплавленный слой металла соединяется с металлической поверхностью путем использования автоматизированных сварочных аппаратов.
Благодаря механизированной технологии сварки и наплавки можно улучшить качество и производительность работ. Автоматизированное оборудование позволяют достичь более высокой точности, т. к. оно может поддерживать определенную скорость, давление и температуру на постоянной основе при сварочных работах. Это позволяет снизить количество ошибок вследствие человеческого фактора.
Механизированная сварка и наплавка – это возможность освободить свою компанию и сотрудников от большого количества обязанностей, ведь автоматизированное оборудование многое сделает за вас. Если вы хотите сократить сроки реализации проектов и повысить эффективность производства лучше отдать предпочтение механизированной сварке, а не ручной.
Технология выполнения
Технология включает в себя несколько этапов. Подробнее о последовательности выполнения механизированных сварочных работ:
1. Первый этап - это подготовка свариваемых деталей и оборудования. Сначала сварщику необходимо очистить поверхности от смазки и грязи с помощью горячего щелочного раствора или горелки. Потом нужно выбрать соответствующий сварочный аппарат или станок. Выбор станка зависит от требований к проекту и возможностей предприятия.
2. Второй этап – предупреждение значительного напряжения и защита от деформации. Для того чтобы избежать появления трещин, специалисту нужно нагреть обрабатываемую деталь до определенной температуры. Выбор температурного режима зависит от габаритов, формы, свойств заготовки и присадки.
3. Третий этап – это настройка сварочного аппарата. Сварщику необходимо выбрать режим сварки, определить значения тока, напряжения, скорость подачи сварочной проволоки.
4. Четвертый этап – размещение деталей. После подготовки и настройки оборудования свариваемые детали нужно правильно расположить и закрепить, чтобы качественно выполнить работу.
5. Пятый этап – непосредственно механизированная сварка, при которой мастер использует автоматический или полуавтоматический сварочный инструмент для реализации задуманного.
6. Шестой этап – проверка качества. После сварки специалисту нужно провести проверку качества сварных соединений, чтобы убедиться, что швы соответствуют требованиям и стандартам. Проверить качество можно путем визуального осмотра.
7. Седьмой этап – конечная обработка. В завершение процесса может потребоваться дополнительная обработка сварных соединений. К примеру, сварщик может выполнить отшлифовку при необходимости.
8. Восьмой этап – документирование. В самом конце составляется соответствующая документация о проведенной работе. Документы должны содержать информацию о проведенных операциях, режиме сварки, использованном оборудовании и других деталях, которые важны для руководства.
Поэтапное выполнение работ – это основа любой технологии (особенно на производстве).
Каждый этап важен и не должен быть пропущен.
Выбор режима наплавки
Качество формирования наплавленного слоя, его химсостав и структура в большой степени определяются режимом наплавки. Поэтому важно серьезно отнестись к его выбору. Режим наплавки определяется количеством электродов, током, напряжением и скоростью электродуги, вылетом электродов, шагом наплавки, а при наплавке тел вращения — смещением с зенита.
Подробнее об этих факторах:
1. Число электродов должно быть подобрано с учетом толщины и ширины наплавляемого слоя, чтобы обеспечить равномерное наплавление и снизить вероятность деформации.
2. Ток и напряжение дуги влияют на глубину проникновения сварочного материала и скорость нанесения. Правильное сочетание этих параметров помогает добиться формирования качественного сварочного шва.
3. Оптимальная скорость перемещения дуги зависит от свариваемого материала и желаемых характеристик сварного соединения. Выбор в пользу слишком низкой или высокой скорости приводит к появлению дефектов.
4. Расстояние между концом электрода и поверхностью свариваемого материала оказывает влияние на глубину проникновения дуги и размеры сварочного шва.
5. Оптимальный шаг наплавки зависит от требуемого размера и формы свариваемой поверхности.
6. При наплавке на вращающиеся тела такие параметры, как смещение с зенита, определяют, будет ли получено равномерное покрытие.
Все вышеперечисленные факторы являются важными и учитываются перед началом работ.
Ниже представлены некоторые распространенные режимы механизированной сварки:
1. Автоматический. Этот режим подразумевает полную автоматизацию процесса с использованием специализированных сварочных аппаратов, которые управляются посредством программного обеспечения (встроенных функций). Этот режим часто используется для сварки на серийном производстве, в рамках которого необходимо создать множество одинаковых деталей.
2. Полуавтоматический. Этот режим подразумевает 50% участие оператора в процессе сварки. При полуавтоматической работе перемещаются лишь электроды, тогда как при автоматической осуществляется механическая подача электродных расходников (лент или проволочек) в область обработки, перемещение деталей и электродов.
Выбор определенного режима сварки зависит от конкретных требований к выполняемой работе и масштаба проекта. К примеру, для маленьких проектов чаще используется полуавтоматический режим сварки.
Виды наплавки
1. Под флюсом. В данном случае дуговая сварка происходит под слоем гранулированного флюса, который защищает электродугу и нагретый металл от воздействия атмосферного воздуха. Этот метод отличается повышенной производительностью и позволяет сваривать толстые металлические пластины.
2. В среде УГ. При этом способе используется углекислый газ для предотвращения окисления расплавленного металла. Механизированные системы позволяют автоматически контролировать подачу сварочной проволоки и газа, что обеспечивает формирование высококачественного сварочного шва.
3. Вибродуговая наплавка. Сущность технологии заключена в постоянной смене стадий горения и короткого замыкания посредством вибрации проволоки.
4. Лазерная сварка. В данном случае лазерный луч используется для нагрева и расплавления металла и сваривания материалов различной толщины. Лазерная наплавка обеспечивает высокую точность выполнения работ, что позволяет сваривать изделия или наносить слой материала, избегая деформаций.
5. Плазменная сварка. В этом случае источником энергии служит плазменный поток. Данный вид сварочных работ характеризуется глубоким проплавлением металла.
6. Индукционная сварка. В этом случае используется принцип индукционного нагрева для расплавления сварочного или наплавочного материала и его нанесения на поверхность детали. В процессе выполнениях данных работ металлическая заготовка нагревается до достаточно высокой температуры путем воздействия переменного магнитного поля, создаваемого индуктором, который обычно представляет собой спиральную катушку или кольцевой элемент. Процесс индукционной наплавки обеспечивает быстрый и точечный нагрев металла, что позволяет избежать деформации.
Эти виды механизированной наплавки используются при выполнении работ в различных отраслях промышленности. Выбор определенного метода зависит от характеристик материалов, требований к качеству и особенностей проекта.
Преимущества
Механизированная сварка (наплавка) обладает рядом преимуществ:
1. Автоматизация. Главное достоинство механизированной сварки - это ее высокая степень автоматизации. Использование специализированных сварочных аппаратов позволяет минимизировать вмешательство человека в процесс сварки, что положительно сказывается на качестве работ.
2. Производительность. Благодаря автоматизации и более высокой скорости выполнения работ механизированная сварка способна обеспечивать значительно большую производительность по сравнению с ручными методами сварки. Это особенно важно при выполнении крупных проектов.
3. Высокое качество. Механизированная сварка помогает достичь более высокого качества сварных соединений (без дефектов).
4. Безопасность. Автоматизация сварочного процесса делают работу операторов более безопасной, сварщик может благодаря автоматизированному оборудованию выполнять те или иные задачи на значительном расстоянии.
5. Точность. Механизированные сварочные аппараты могут иметь множество встроенных функций для выполнения определенных операций с высокой степенью точности.
6. Адаптивность. Механизированная сварка может быть применена для соединения различных типов металлов и сплавов, что делает ее универсальной. Она подходит для выполнения абсолютно разных промышленных задач.
7. Работа в сложных условиях. Механизированная сварка позволяет выполнять сварочные операции в труднодоступных и иногда даже в опасных местах.
8. Контроль. Многие сварочные аппараты, предназначенные для механизированной сварки, оборудованы сенсорами, которые позволяют отслеживать параметры сварки в режиме реального времени и корректировать процесс для достижения оптимальных результатов.
9. Минимальные расходы. Механизированная сварка позволяет сократить затраты на материалы, а также уменьшить количество бракованных изделий, что способствует повышению эффективности производства.
10. Мобильность. Существуют удобные и компактные модели механизированных сварочных аппаратов, что облегчает процесс их перемещения на различные участки производства.
Именно из-за большого количества преимуществ данный вид сварки так ценится на производстве. Огромное количество специалистов уже не знают, как обойтись без данного способа наплавки.
Особенности технологии механизированной сварки и наплавки
Ниже рассмотрены особенности механизированной сварки и наплавки:
1. Различные режимы и методы. Механизированная сварка/ наплавка включает в себя разные режимы работ (при которых могут использоваться разные методы выполнения тех или иных рабочих задач). Благодаря этому можно выполнить любой проект за короткий срок.
2. Системы контроля. Автоматизированные системы позволяют легко контролировать температуру процесса сварки и наплавки, что позволяет получить на выходе высококачественные детали.
3. Изменение состава и свойств. Механизированные методы сварки/наплавки позволяют в широких пределах регулировать состав и свойства наплавленного металла.
4. Эффективность и производительность. Механизированная сварка и наплавка значительно повышают эффективность и производительность работ, что особенно важно в промышленных условиях с высоким объемом производства.
5. Минимум ошибок и дефектов. Благодаря высокому уровню контроля при использовании такой сварки можно избежать деформации деталей, что снижает необходимость в повторной обработке.
6. Равномерное нанесение материала. Автоматизированные аппараты обеспечивают равномерное распределение сварочного материала или наплавочного слоя, что приводит к более качественному результату.
7. Работа под любым углом. Некоторые сварочные агрегаты позволяют осуществлять сварку под различными углами, что очень важно при реализации сложного проекта.
Все эти особенности делают механизированную сварку/ наплавку незаменимым технологическим процессом.
Оборудование
Оборудование для механизированных сварочных работ разнообразно. Однако чаще всего на производстве используются:
1. Манипуляторы сварочные (с ручным приводом и без). Они представляют собой автоматизированное оборудование, которое устанавливается на рабочую поверхность и способно перемещать сварочную головку по заданным координатам.
2. Механизированные сварочные тракторы. Представляют собой универсальные машины для сварки. Они оборудованы сварочными горелками и могут двигаться по заранее заданной траектории, выполняя работу на больших плоских поверхностях.
3. Автоматизированные аппараты для вибродуговой наплавки. Это специальные сварочные устройства, которые являются основной частью вибродуговых установок. Они используются для наплавки маленьких цилиндрических деталей.
4. Лазерные и плазменные аппараты. Лазерные и плазменные машины позволяют выполнить высокоточную сварку и наплавку с использованием лазерного или плазменного потока.
5. Механизированные расточные станки. Такие устройства обеспечивают точную обработку поверхности деталей перед наплавкой или после сварки для получения гладкой поверхности. Они бывают как крупногабаритными, так и портативными, которые можно переместить к месту обработки деталей. Расточные станки предназначены для формирования отверстий, обработки поверхностей и создания точных геометрических форм.
6. Расточно-наплавочные комплексы. Это универсальные устройства, которые соединяют в себе функции расточки и наплавки, что позволяет выполнить полный цикл обработки на одной машине.
7. Индукционные аппараты для наплавки. Это оборудование, использующее принцип индукционного нагрева для наплавки материала. Они обеспечивают быстрое и точное распределение тепла, что позволяет получить высококачественный результат.
Все вышеперечисленные устройства играют важную роль в сварочных работах. Без них не обходится практически ни один мастер. Они позволяют обрабатывать и восстанавливать детали с высокой точностью и эффективностью, что делает их востребованными в различных отраслях промышленности.
Помимо базового оборудования, также существует и дополнительное. К примеру, сварщики используют в процессе работы сварочные пистолеты, ножницы для резки металла, оснастки расточки и проточки и другие инструменты.
Оснастка расточки и проточки используется для обработки поверхностей и отверстий в различных материалах. Она позволяет быстро и эффективно выполнять работу с минимальными усилиями. С ее помощью можно проточить углубления различной глубины и диаметра, а также создавать шпонки, канавки, калибровочные отверстия. Оснастка может быть различной формы и размеров, в зависимости от требований проекта.
Использование данного приспособления позволяет существенно повысить производительность работы, сократить время обработки и снизить вероятность появления ошибок. Если вы часто используете расточные, фрезерные ЧПУ, вам стоит найти подходящую оснастку для них (если вам важен результат на выходе).
Заказать качественные приспособления можно в интернет-магазине НашиСтанки.
На сайте представлена оснастка для МНС-59 и для расточно-наплавочных комплексов.
Комплект для расточки и проточки состоит из режущих инструментов, направляющих и фиксирующих элементов. Оснастка разработана с учетом конструктивных особенностей оборудования и требований, предъявляемых к нему.
Все оснастки, представленные на сайте, прошли проверку качества. Заказывать в данном интернет-магазине можно с уверенностью, что вы получите качественный товар в установленный срок.
Заключение
Также она имеет множество других плюсов.
Одним из главных преимуществ механизированной сварки является повышение производительности. Автоматизированные системы позволяют выполнять работу быстрее и качественнее, чем при ручной сварке. Это особенно важно на производстве, когда каждая минута имеет значение.
Благодаря механизированной сварке/наплавке компании могут сократить время и трудозатраты на изготовление и сборку изделий.
Кроме того, преимуществом данного вида сварки является повышение качества. Механизированная наплавка способствует повышению качества сварных соединений и снижению вероятности допущения ошибок.
При ручной сварке существует вероятность получения на выходе плохих сварных соединений и деформации некоторых изделий из-за человеческого фактора, в то время как автоматизированная система редко ошибается (только в случае сбоя программного обеспечения или выхода из строя основных компонентов).